The average cost of lithium-ion battery cells soared to an estimated $160 per kilowatt-hour in the first quarter of 2022 from about $105 last year—an increase of over 50 percent—due to supply chain disruptions, shortages of materials, sanctions on Russian metals and investor speculation. Most manufacturers have passed higher costs on to consumers with double-digit price increases for electric vehicles. For a smaller vehicle like the Hongguang Mini, the best-selling electric vehicle in China, the higher battery costs added almost $1,500—about 30 percent of the sticker price for the 27 horsepower microcar. Because margins in the battery industry are wafer thin, cost increases will be passed onto carmakers and, in most cases, customers.
In 2021, the $105 per kilowatt hour average cost was a huge decline from the cost of over $7,500 in 1991. Automakers and suppliers in mining, refining and battery cell production are making investments to diversify raw material sources. The industry was looking toward a battery cell cost threshold of $100 per kilowatt-hour, as a signal electric vehicles were reaching price parity with fossil-fuel equivalents.
Costs of nickel, lithium and cobalt—key supplies for battery manufacturing—have been rising due to world demand. With Russia accounting for 11 percent of the world’s nickel, and supply chains stretched, the Russian invasion of Ukraine resulted in the price of those commodities skyrocketing. The value of those three metals required in a 60 kilowatt hour battery, sufficient for a large sport utility automobile, increased from $1,395 to over $7,400 in early March—an increase of 430 percent. Along with battery materials costs, prices of aluminum, metal and copper have also increased.
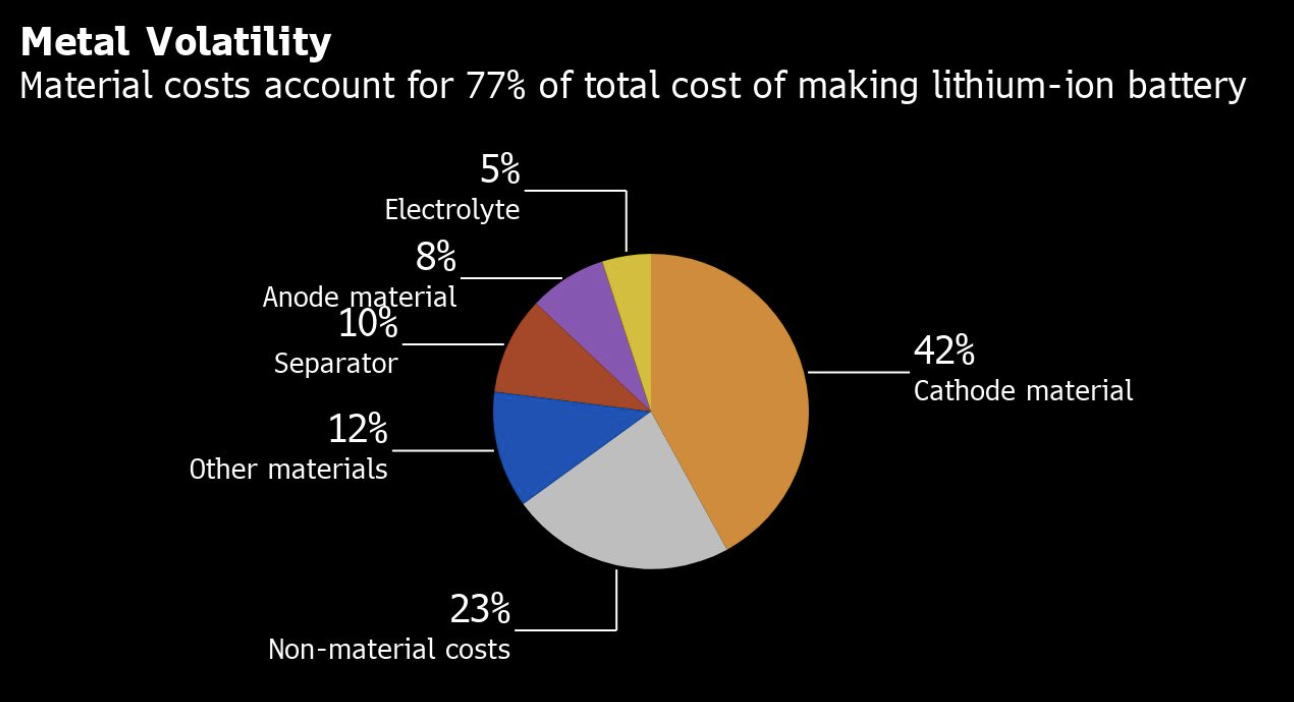
Batteries account for about 30 to 40 percent of the price of an electric vehicle. Before Russia’s invasion of Ukraine, Dan Ives, who covers EV stocks for Wedbush Securities, estimated that a shortage of nickel and other rising costs could force electric vehicle makers to raise prices by $1,200 per vehicle.
According to Bloomberg New Energy Finance’s (BNEF) annual battery price survey, lithium-ion battery pack prices averaged $132 per kilowatt hour in 2021—down from $140 per kilowatt hour in 2020. Inside each electric vehicle battery pack are multiple interconnected modules made up of tens to hundreds of rechargeable Lithium-ion cells. Collectively, these cells make up roughly 77 percent of the total cost of an average battery pack, or about $101 per kilowatt hour. On a regional basis, in 2021, battery pack prices were cheapest in China, at $111 per kilowatt hour and helps explain why China manufactures 80 percent of the world’s battery cells (see graphic below). Battery packs in the United States and Europe cost 40 percent and 60 percent more, respectively, reflecting the relative immaturity of the markets, the diverse range of applications and low volume and bespoke orders.
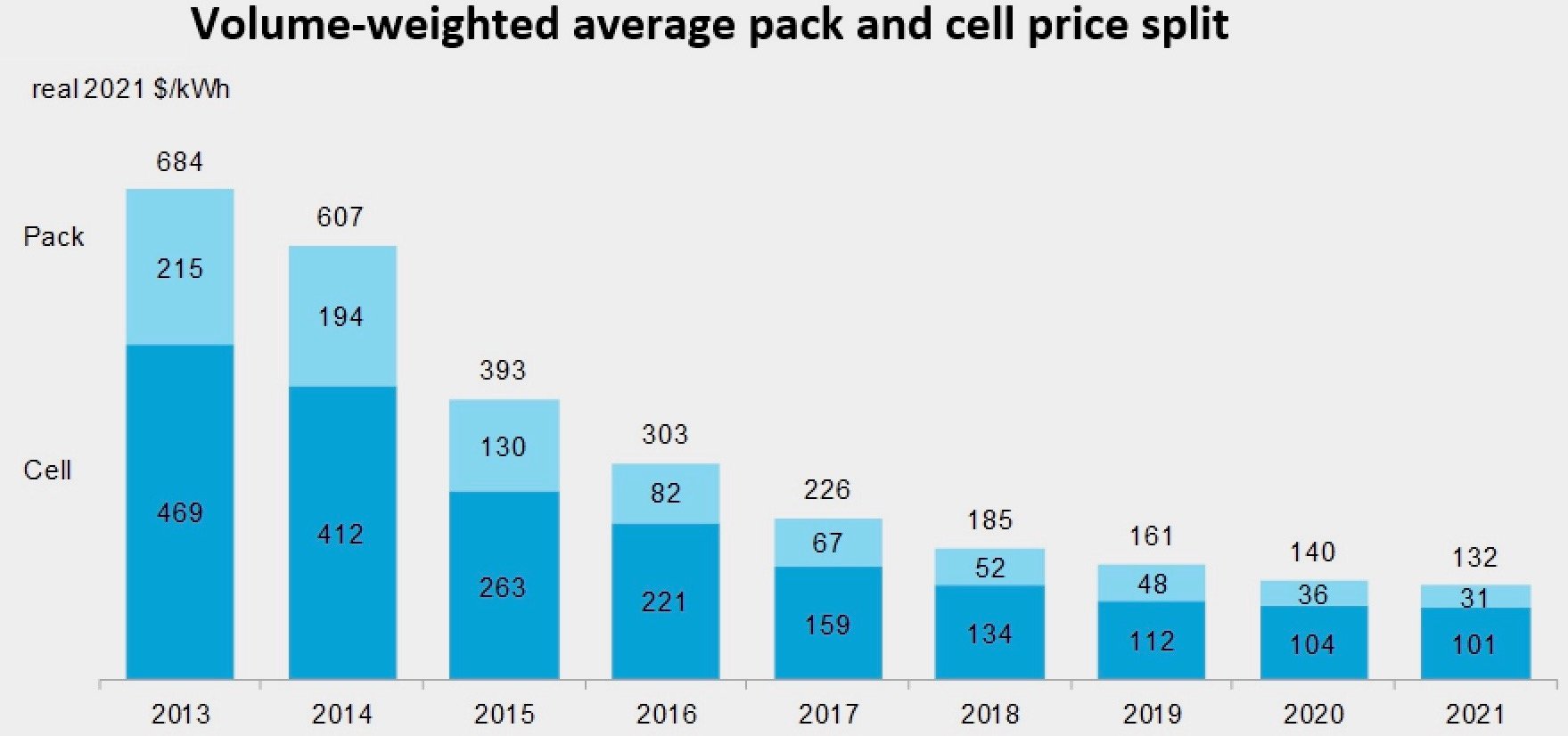
The Cost of a Battery Cell
According to data from BloombergNEF, the cost of each cell’s cathode is more than half of the overall cell cost, as shown in the graphic below. The cathode is the positively charged electrode of the battery. When a battery is discharged, both electrons and positively-charged molecules flow from the anode to the cathode, which stores them until the battery is recharged. Cathodes effectively determine the performance, range, and thermal safety of a battery, making them one of the most important components. They are composed of various metals (in refined forms) depending on cell chemistry, typically including lithium and nickel. The commodities in the cathode, along with those in other parts of the cell, account for about 40 percent of the overall cell cost.
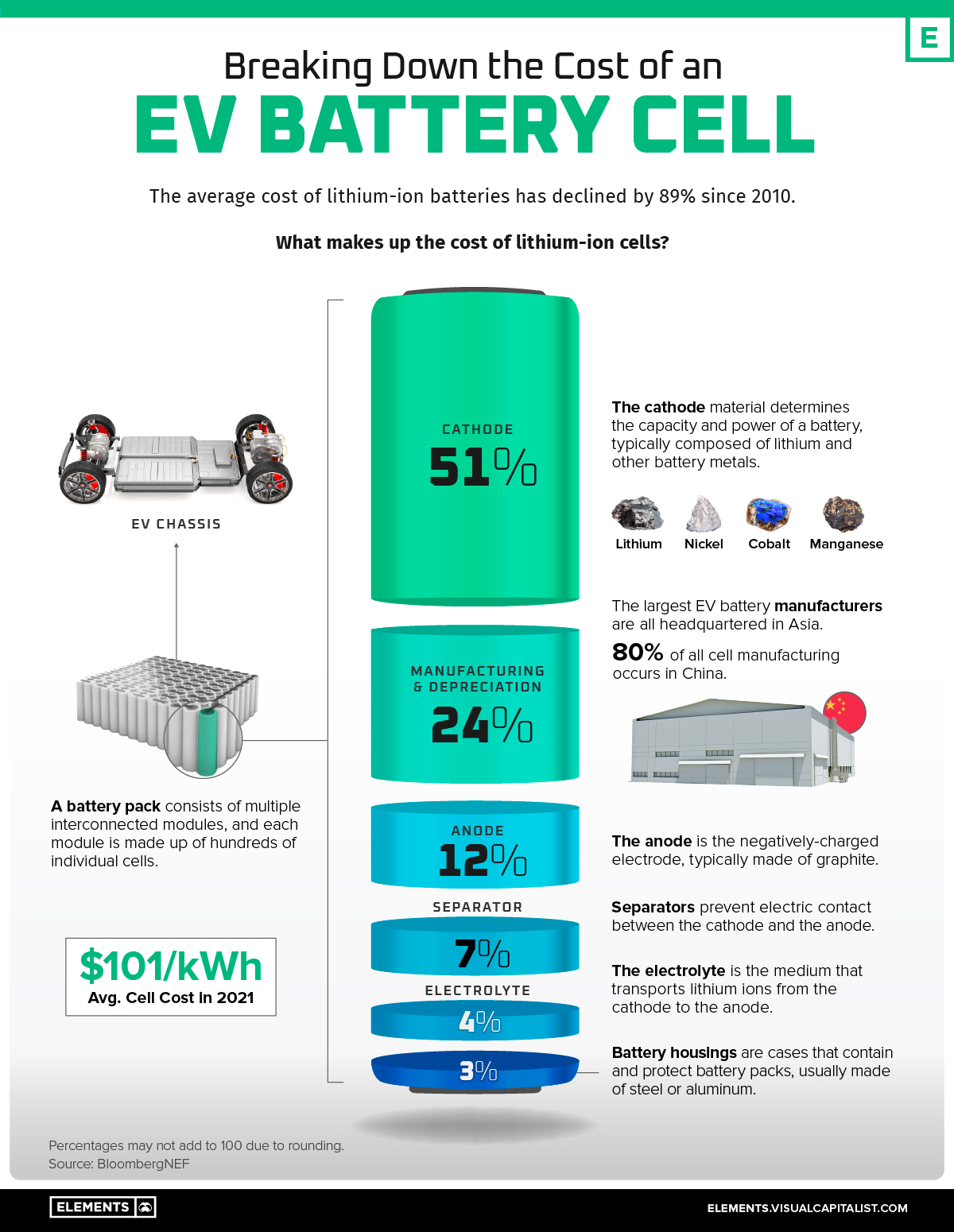
Components outside of the cathode make up the other 49 percent of a cell’s cost. The manufacturing process, which involves producing the electrodes, assembling the different components, and finishing the cell, makes up 24 percent of the total cost. The anode—another significant component of the battery—makes up 12 percent of the total cost. The anode in a lithium-ion cell is typically made of natural or synthetic graphite, which tends to be less expensive than other battery commodities, but upon which the United States is 100 percent dependent on imports. China produces 60 percent of the world’s graphite.
Conclusion
The cost of electric vehicle battery cells has increased by over 50 percent this year as material shortages, supply chain issues and the Russian invasion of Ukraine raised their prices. Most manufacturers are passing those costs onto consumers since there is little room for cost absorption by cell producers. The higher costs will make it more difficult for President Biden to reach his goal of electric vehicles being 50 percent of new car sales by 2030, and will hit consumers hard who are forced by government policies to purchase electric vehicles.